RBS(Random Box Stack system)
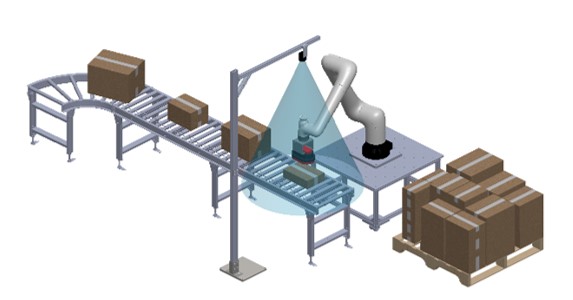
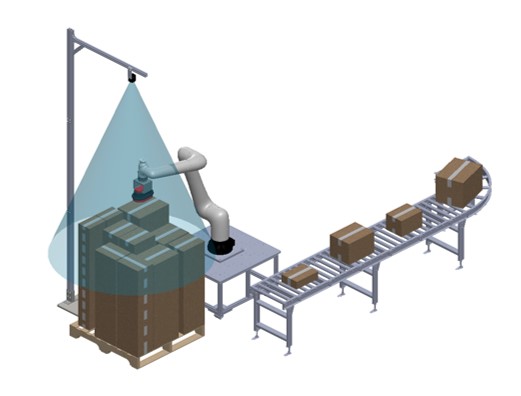
Introduction of RBS
This is a program that recognizes the size and location of irregular boxes using a 3D camera and uses artificial intelligence to make robot palletize and depalletize them.
Competence of RBS
No additional teaching is required from the user. Even if the box changes, the camera automatically recognizes the size of the box and allows you to work.
Cameras are cheap. It is much cheaper than existing structured light cameras or stereo cameras, but is also price competitive as it uses an AI-enabled TOF (Time Of Flight) 3D camera.
Applicable to all robots. Because it communicates with robots directly, it can be applied to all robots regardless of robot company or type.
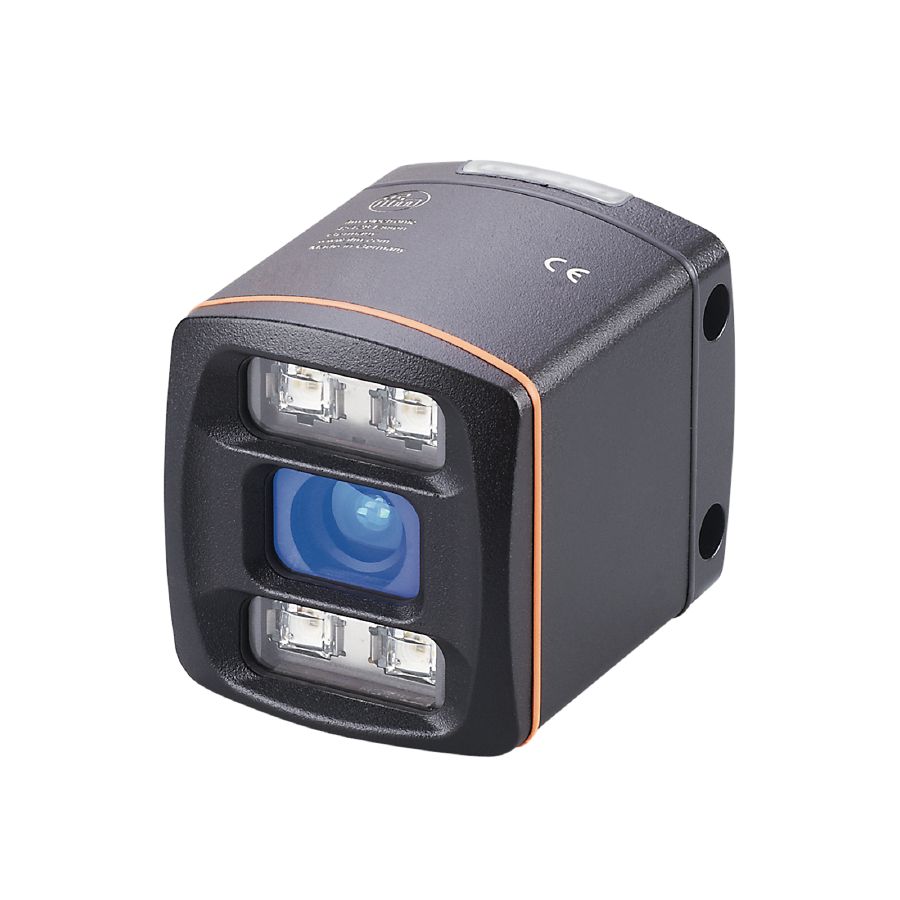
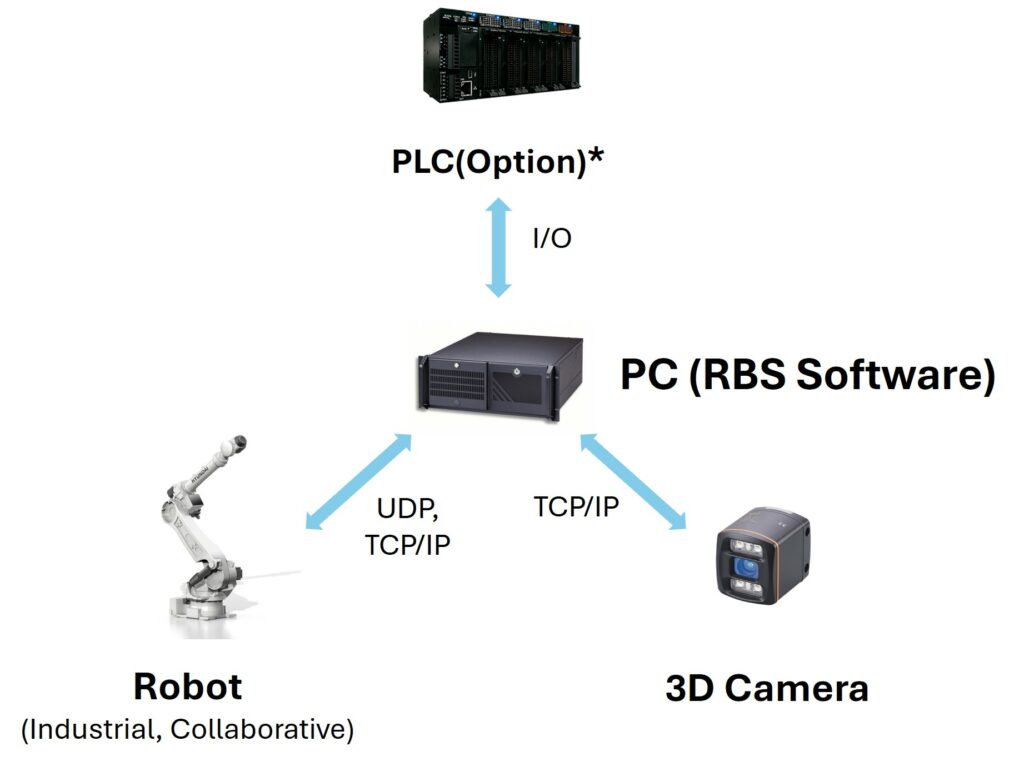
System configuration
Since it does not go through PLC, communication speed is fast and system configuration is simple
Technology of RBS
Algorithm & Simulation
RBS ensures real-time responsiveness by delivering results to the robot within 0.5 seconds, and has a stacking algorithm that prevents boxes from falling over, allowing boxes to be stably stacked high over 1.8m.
Additionally, to maximize space efficiency, users can choose whether to stack boxes horizontally, vertically, or in a mixed manner.
We also have simulation technology to verify algorithms.
Application example #1
RBS with Hyundai YS080L
In November 2023, 1 Set of RBS was delivered to ‘L’ Logistics Company located in Cheongju, Chungcheongbuk-do, and has been successfully operated to date. Here, more than 10 types of delivery boxes are supplied from one conveyor line, and RBS stacks the randomly supplied boxes using an algorithm optimized for the designated roll container in a space-efficient manner so that they do not fall over. After loading, the roll container moves to the loading dock.